Kate Shanks started working with CHESS in 2009 as a user; today she runs the FAST (Forming and Shaping Technology,) beamline as a Staff Scientist. FAST’s mission is to investigate, understand, and solve performance and processing issues in the field of structural materials.
The FAST beamline focuses on high energy monochromatic techniques in diffraction and imaging. These techniques are applied to in situ sample environments in order to investigate the microstructure of materials while they are being mechanically loaded, thermally cycled, and/or being processed or built up (as in 3D printing).
Experiments at FAST primarily focus on structural materials such as cements, ceramics, and various alloy materials whose primary purpose is to bear a mechanical load. Structural materials differ from functional materials, another type of material studied at other CHESS beamlines, which are analyzed for their functions such as electrical or magnetic properties. There is also the potential to study materials like ceramics or soils at FAST.
At FAST, the main goal is to understand how a material’s microstructure relates to its mechanical properties, like strength, brittleness or ductility and potential for failure. Shanks explains,
“The ultimate goal is to develop predictive models to know when materials are going to fail, so we have a solid idea of, say, the operational lifetime of engineering components. And potentially how to design materials to have enhanced mechanical properties.”
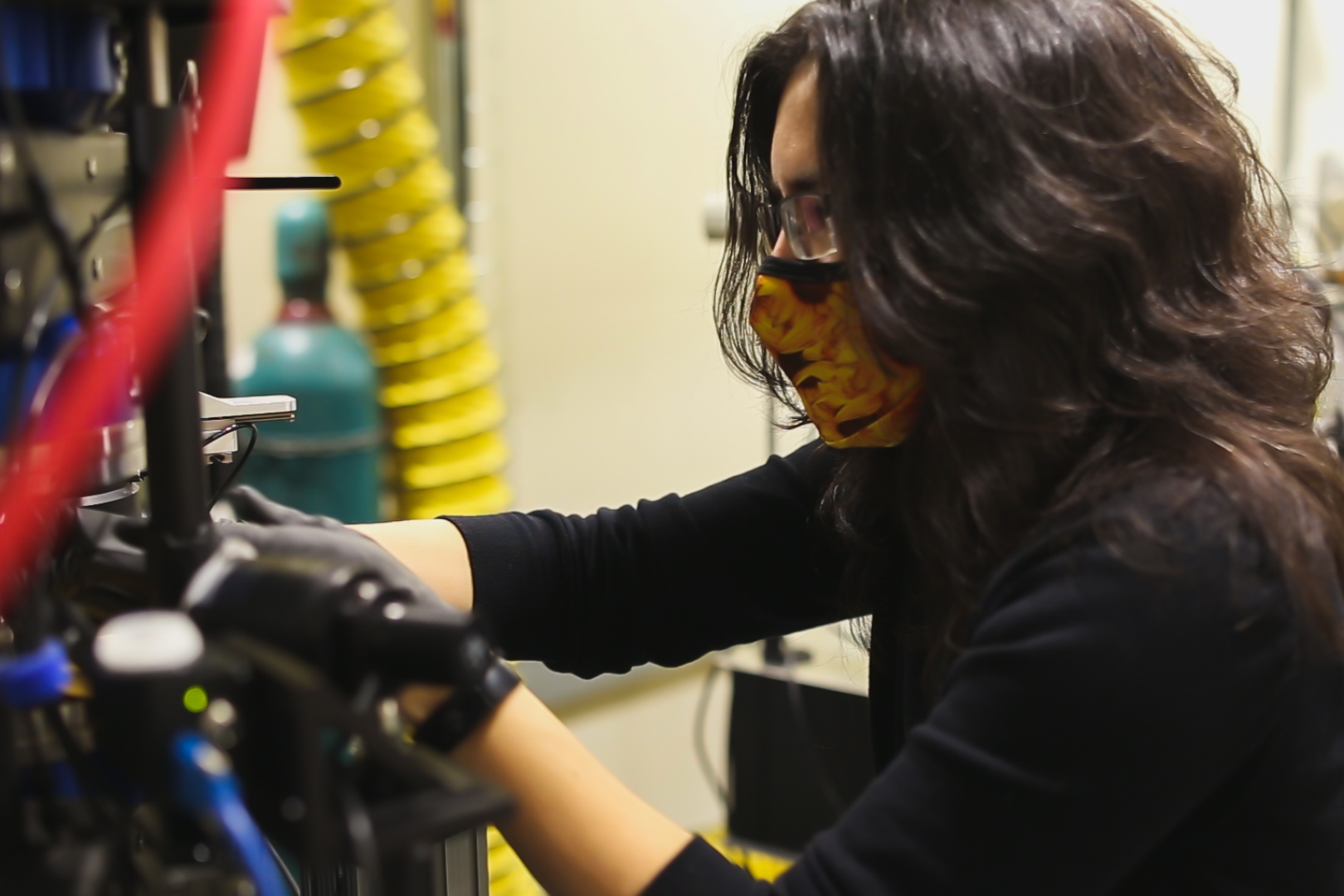
The experiments that happen at FAST can have a major impact on everyday lives. Airplane parts, medical device components, and building materials are prime examples of items that can be improved when we have a better understanding of when that part is going to fail, or how its durability can be increased and costs reduced from the start. Predictive models for material performance can go a long way toward making better engineering components.
A bread-and-butter experiment at FAST involves looking at the diffraction or tomography of a sample as it’s placed under a mechanical load (either compressed or stretched). A recent example of such an experiment that Shanks found particularly exciting? Moon cement. Researchers are considering the potential to build infrastructure on the moon, but it would be cost-prohibitive to transport all the construction materials. So an alternate possibility emerges: building structures there with the abundant materials at hand - Moon rocks! Researchers from Penn State recently brought cement made from synthetic moon rocks (real moon rocks are too precious and expensive to use) to the FAST beamline to study how its microstructure changed as the cement was crushed.
Though much of the research at FAST thus far has involved pre-made materials, another area that Shanks is excited about delving into further is the time-resolved study of additive manufacturing, known commonly as 3D printing. “Having robust, reliable and well-understood additive manufacturing techniques for metal alloys would open up a lot of new opportunities and ways to build engineering components,” explains Shanks. Additive manufacturing introduces the potential to create unique components on the fly and at lower cost, just by loading a design and pressing “go”, rather than relying on an entire supply chain being in place.
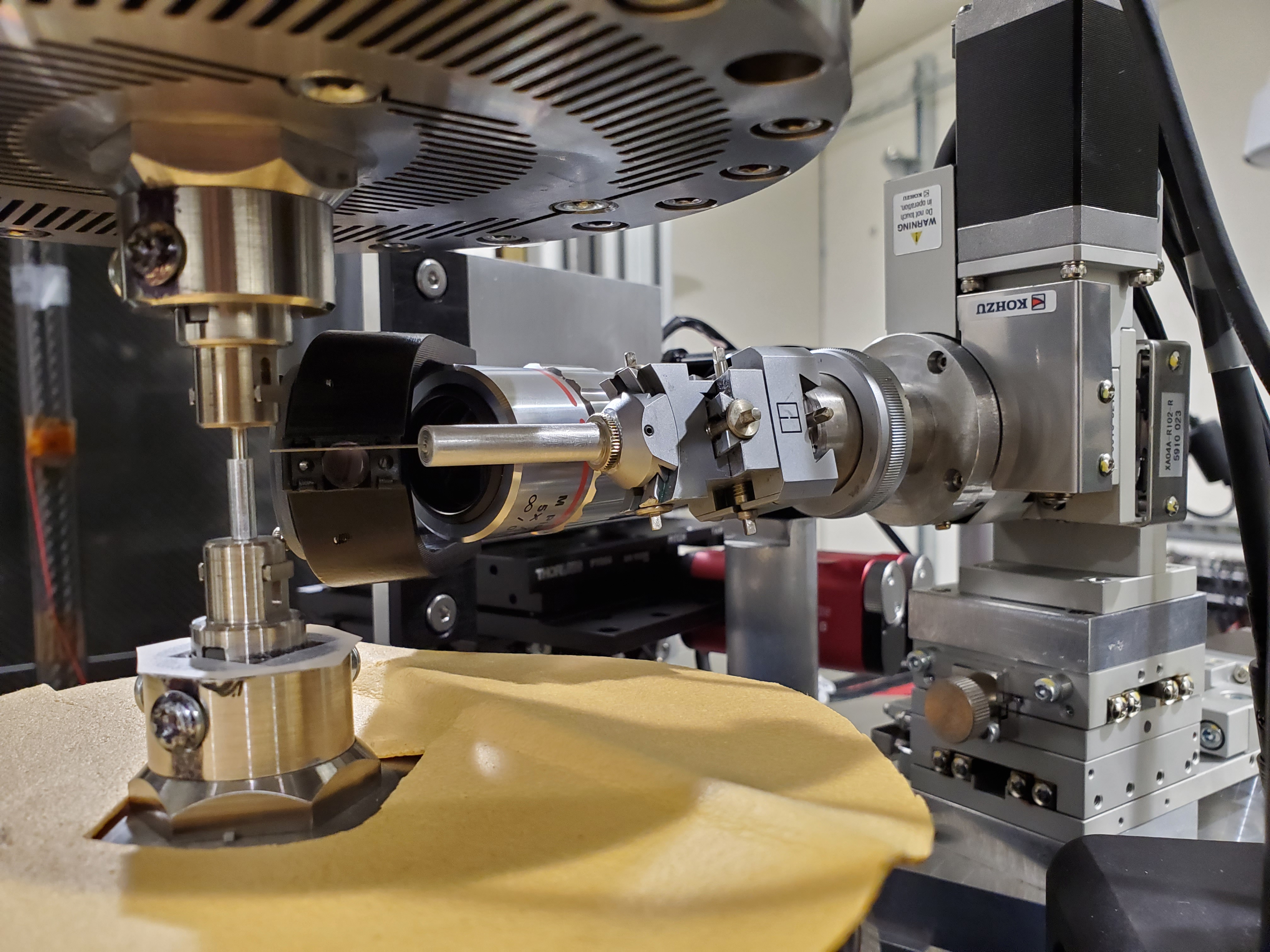
However, in order for additive manufacturing to be viable, the composition and microstructure of the outputs need to be rigorously tested, since they are very different from components made from traditional manufacturing techniques. The FAST beamline is equipped with x-rays of high-enough energy, as well as bright-enough x-rays, and will soon have fast-enough detectors, to put additive manufacturing chambers into the beamline and watch in real-time as a 3D-printed part is built-up. Some research groups have brought custom-built 3D printing chambers to FAST for preliminary experiments, and the potential for future projects is growing quickly. This process allows researchers to see how the microstructure evolves by the millisecond and potentially down to the nanosecond.
In 2020, CHEXS beamlines introduced remote access, allowing researchers to take advantage of our facilities and support staff from anywhere in the world. As Shanks explained, the experience of being at the beamline is very unique and immersive, such that many users had trouble imagining how remote access could be successful. But Shanks relished in the success, saying that “in the user groups I’ve been working with they keep saying, ‘oh I was kind of skeptical about this, but it’s like we’re at the beamline!’ So that feels like a big success and it’s completely to the credit of the CLASSE IT staff and the operational staff that has made remote access run really smoothly, and it’s a really good approximation of being here.” The success of remote access at CHEXS opens up the beamline to researchers who otherwise may not be able to travel to Ithaca, and Shanks is excited for the increased accessibility.

“You can’t be a scientist by yourself.”
That’s the motto Shanks learned from a physics professor of hers. “I really love working as part of a big team, getting to work with all these different user groups, there’s always something new to learn or something new to try, and you get to do those things with experts and that is just a fantastic place to work.” The other exciting part of working at CHEXS for Shanks are the experiments themselves. “It’s really fun to bring together all the tools and infrastructure and instrumentation...to enable someone to do a measurement that they couldn’t do before. That’s just really exciting as a scientist!”
And what does the future look like at FAST? “Literally, the future at FAST is brighter,” she laughs. But it’s true. In the coming year there are plans for upgrades to the upstream optics, which will give FAST a brighter monochromatic beam. This will enable more time-resolved studies of materials processing, more in situ experiments, and more realistic conditions to help mimic how materials actually behave in the real world.