What is the discovery?
In a recent paper, a team of researchers lead by Don Brown of Los Alamos National Laboratory have used high energy x-ray diffraction to track the evolution of the microstructure in additively manufactured Ti-6Al-4V during heat treatments. Beginning with as-built components prepared via the laser powder bed fusion technique, the team observed significant modification of the crystalline phases, the internal stresses, the dislocation density, and the vanadium distribution as the samples were heated up to temperatures greater than 1000 K. Specifically, the dislocation density and intergranular stress decrease significantly at 770K, and a phase transformation occurs between 918K and 1281K. Heat treatment causes the microstructure of the additively manufactured alloy to more closely resemble traditionally wrought material, although the grain size, vanadium distribution, and texture remain quite different. Diffraction patterns from as-built powder-bed material (PB), traditionally wrought materials (WR), and PB material that has been heat-treated at 1043K are shown in the figure at right.

Why is it important?
Ti-6Al-4V (also known as Ti64) is strong and lightweight with good corrosion resistance. For these reasons, Ti64 is an important alloy for the aerospace industry. The desirable properties of traditionally wrought Ti64 result from the equilibrium microstructure, which forms under slow cooling. Conversely, components made via additive manufacturing typically exhibit poor structural properties arising from a non-equilibrium microstructure which forms under rapid cooling. The goal of the research reported here is to understand and design post-build heat treatments that can restore the desired structural properties to additively manufactured components. If a heat treatment procedure can be found which recreates the as-wrought microstructure, it would enable cost-effective advanced manufacturing of complex components in the future.
Why did this research need CHEXS?
This research made use of the FAST beamline at CHEXS, which is dedicated to studies of structural materials processing and performance. High flux, high-energy x-ray beams were used to penetrate through the bulk of the metallic alloy samples. The in-situ heater for high energy diffraction, large-format area detectors, and computational resources of FAST were all essential for the success of this research.
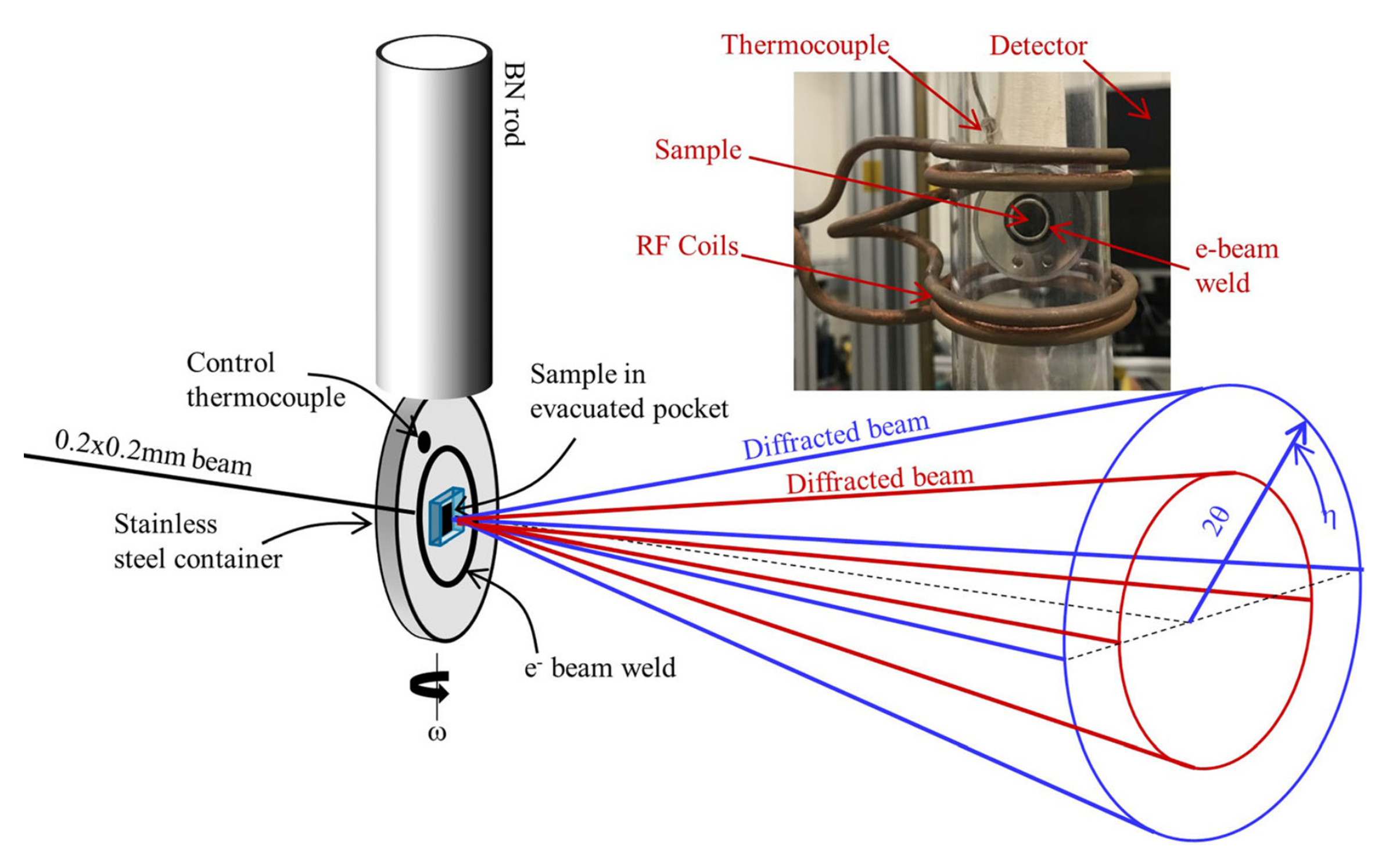
How was the work funded?
Los Alamos National Laboratory: US Dept of Energy, contract DE-AC52-06NA25396
Lawrence Livermore National Laboratory: US Dept of Energy, contract DE-AC52-07NA27344
National Institute of Standards and Technology: US Dept of Commerce
The Center for High Energy X-ray Sciences (CHEXS), NSF (DMR-1829070)
Reference:
Evolution of the Microstructure of Laser Powder Bed Fusion Ti-6Al-4V During Post-Build Heat Treatment
DW Brown, V Anghel, L Balogh, B Clausen, NS Johnson, RM Martinez, DC Pagan, G Rafailov, L Ravkov, M Strantza, & E Zepeda-Alarcon
Metallurgical and Materials Transactions A, 52 5165–5181 (2021); https://doi.org/10.1007/s11661-021-06455-7