Recently, researchers and manufacturers have become interested in adding fiber reinforcement into polymer and ceramic materials produced by additive manufacturing (AM) to produce high-performance composite materials with exceptional strength in complex geometries. However, the amount of fiber that can be incorporated into these materials is limited by the propensity of fibers to clog the nozzle during deposition.
What did the scientists discover?
These results revealed three different mechanisms for clog formation. Specific clogging mechanisms included log-jam pileup of misoriented fibers near the nozzle tip, the lodging of entangled fibers in the nozzle tip, and the accumulation of misoriented fibers at step-like reductions in the nozzle profile. Together, these show that how a nozzle clogs depends substantially on the fiber volume fraction, fiber length and nozzle geometry.
What are the broader impacts of the work?
Even though the AM community had identified fiber clogging as a key obstacle to printing high-performance composites with high volume fractions, the mechanisms that contribute to fiber clogging were not known. To the authors’ knowledge, only one study has previously studied the clogging behavior of a polymer reinforced with spherical particles. We show that the clogging mechanisms are very different for fiber reinforced inks. Armed with this new knowledge, engineers can now rationally design inks and nozzles to prevent nozzle clogging during printing.
Why is this important?
Additive manufacturing has the potential to revolutionize aerospace manufacturing due to its abilities to (i) to produce parts with previously unmanufacturable shapes, (ii) tuning material properties within the part, and (iii) combining multiple materials in previously inaccessible ways. This work enhances the reliability of the AM process, which is a key obstacle to printing production parts for aerospace applications.
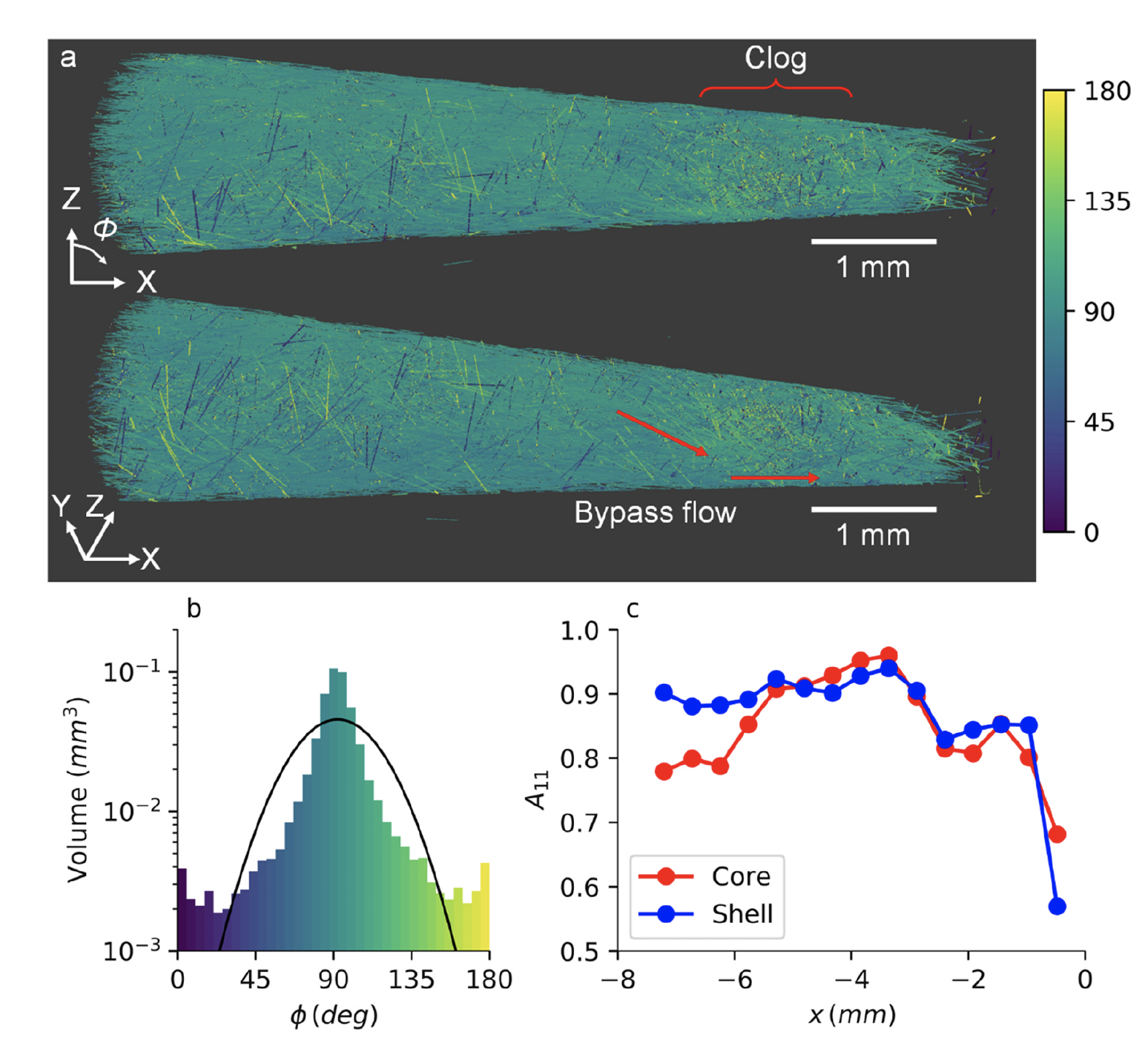
Why did this research need MSN-C & CHESS?
The high x-ray flux at MSN-C enabled imaging at over 25 frames per second, which is hundreds of times faster than can be done with laboratory equipment. This allowed us to visualize dynamic flow events and clogging behavior inside the nozzle with high spatial and temporal resolution.
How was the work funded?
Data was collected at the Materials Solutions Network at CHESS (MSN-C), which is supported by the Air Force Research Laboratory (AFRL) under award FA8650-19-2-5220. Data analysis was performed at AFRL with funding from an NRC Research Associateship, USRA AFRL Summer Scholars Fellowship (under award FA9453-18-2-0009), and the University of Tennessee.
Reference
Brendan P. Croom, Andrew Abbott, James W. Kemp, Lisa Rueschhoff, Louisa Smieska, Arthur Woll, Stanislav Stoupin, Hilmar Koerner, Mechanics of nozzle clogging during direct ink writing of fiber-reinforced composites, Additive Manufacturing, Volume 37, 2021,101701, ISSN 2214-8604, https://doi.org/10.1016/j.addma.2020.101701