Recent advances have enabled room-temperature additive manufacturing (AM) of carbon fiber composite parts with high stiffness and strength. An AM method called direct ink write (DIW) is used, wherein a self-supporting fluid material – in this case, an epoxy resin composite – is extruded through a nozzle to print parts with custom shapes, which are thermally cured after printing. To achieve the superior properties required by aerospace applications, characterization of the morphology is crucial, but has proven exceedingly difficult to date. In this work, we demonstrate the power of scanning microbeam X-ray scattering to provide new insights about the morphology of these printed materials.
What did the scientists discover?
Scanning microbeam small- and wide-angle X-ray scattering was performed on cross-sections of printed parts, where a 2.5 x 10 um beam was rastered across several mm2 of the samples. Maps of the nanoclay orientation revealed that the orientation is strongly influenced by the printing process. The edges of the printed roads contained strongly oriented nanoclay due to the shear fields in the nozzle and upon deposition. From this data, the shapes of the roads could be visualized – to date, no other experimental method can do this. Upon adding carbon fibers to the formulation, we directly visualized the carbon fibers and overlayed them on the nanoclay orientation map. The carbon fibers did not perturb the nanoclay morphology or the road structure, but its distribution was not uniform across roads. Finally, we qualitatively reproduced a polarized optical micrograph based on the X-ray map, revealing the underlying structure giving rise to the features observed in the micrograph.
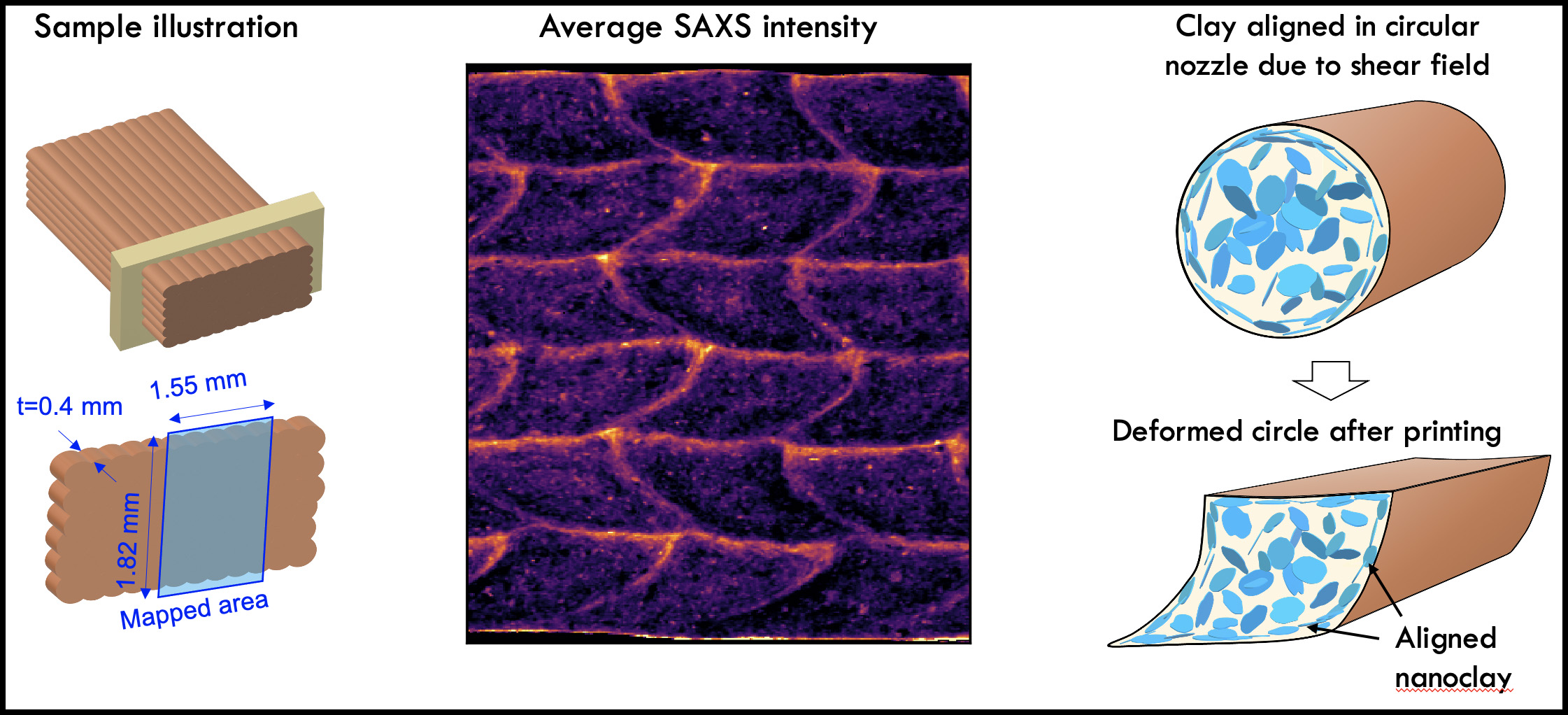
What are the broader impacts of the work?
This work demonstrates the power of scanning microbeam X-ray scattering to reveal the morphology of printed materials in general. Specifically, we showed that the road structure of printed epoxy/nanoclay composites can be visualized with this technique, enabling optimization of the road structure with respect to properties. The ability to map the carbon fiber positions onto the road structure will inform future work to optimize carbon fiber distribution and orientation.
Why is this important?
Additive manufacturing has the potential to revolutionize aerospace manufacturing due to its abilities to (i) to produce parts with previously unmanufacturable shapes, (ii) adjust material properties within the part, e.g. creating property gradients, and (iii) combining multiple materials in previously inaccessible ways. The deep characterization provided by scattering microbeam X-ray scattering is a major step forward in understanding these printed materials. Future work will exploit this characterization to understand the relationship between morphology and properties.
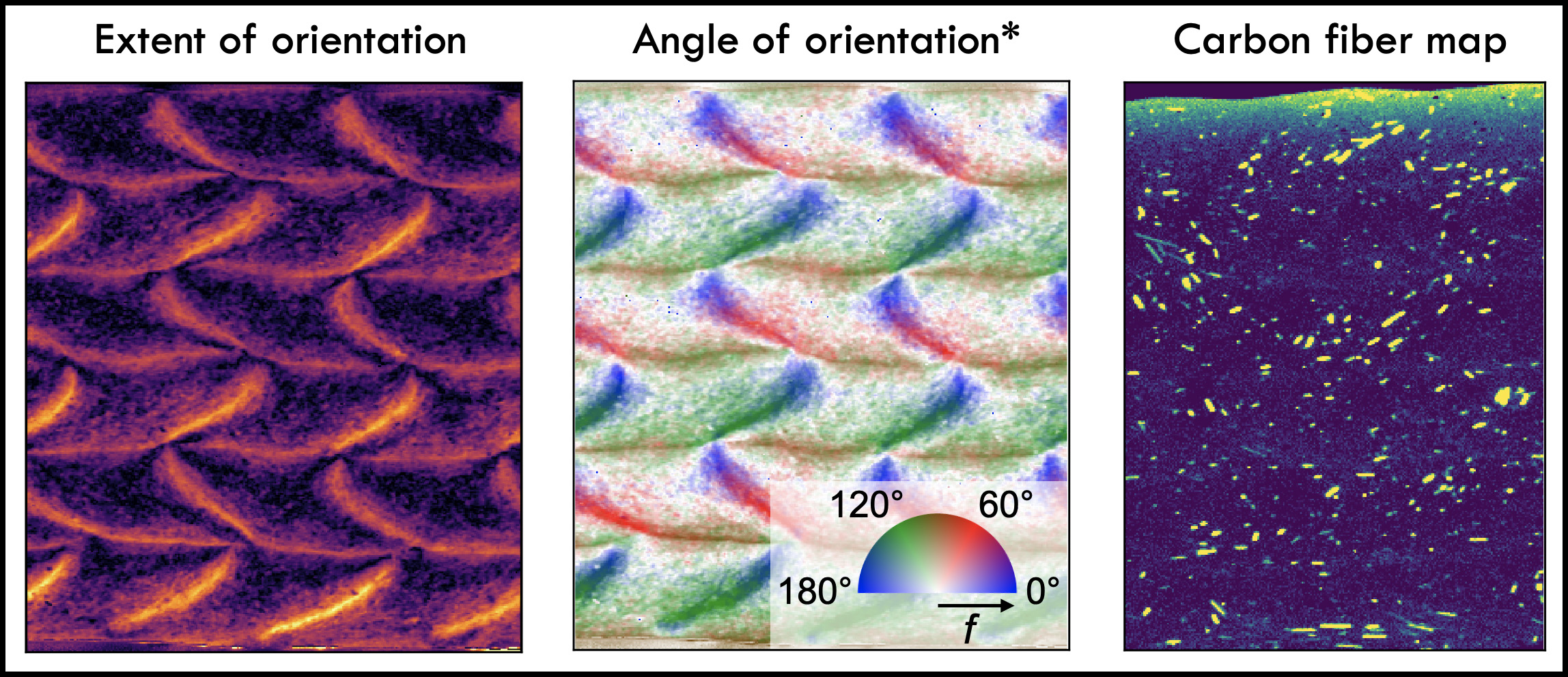
Why did this research need MSN-C & CHESS?
Scanning microbeam X-ray scattering can only be performed at a synchrotron with high brilliance X-rays such as CHESS. Further, the Functional Materials Beamline has state-of-the-art focusing optics to achieve the small beam size (2.5 x 10 um) required for this technique. This work would be impossible at existing Department of Defense facilities.
How was the work funded?
Data was collected at the Materials Solutions Network at CHESS (MSN-C), which is supported by the Air Force Research Laboratory (AFRL) under award FA8650-19-2-5220. Data analysis was performed at AFRL with funding from an NRC Research Associateship and AFOSR under the Low Density Portfolio # 17RXCOR436. The samples were made at the University of Tennesse, Knoxville with support from NSF under grant no. CMMI-1825815, and Honeywell Federal Manufacturing and Technologies through Contract DE-NA0002839.
Reference
Edward B. Trigg, Nadim S. Hmeidat, Louisa M. Smieska, Arthur R. Woll, Brett G. Compton, Hilmar Koerner, Revealing filler morphology in 3D-printed thermoset nanocomposites by scanning microbeam X-ray scattering, Additive Manufacturing, Volume 37, 2021, 101729, ISSN 2214-8604, https://doi.org/10.1016/j.addma.2020.101729.
For further information, please contact Hilmar Koener.